
Book
American Engravers
The 21st Century
by
C. Roger Bleile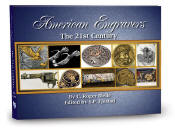
| |
GAME SCENE – Also known as a hunting scene, the game scene
featuring wildlife, dogs, and sometimes hunters in a rustic setting has
been the stock in trade of arms engravers for many centuries. Game
scenes can be line cut, bulino, low relief, high relief, or inlaid with
precious metal. Italian: scene di caccia or paesaggi, German;
jagdszenen, French: scènes de chasse, Spanish: escena de caza.
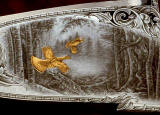
Pictured from left is a simple line cut game scene on a German shotgun
from 1943. Next, the gamescene features raised gold inlayed grouse and
at right a highly detailed "bulino" game scene on the sidelock of an
Italian Famars by Steve Lindsay.
|
GERMAN SCROLL – Small to medium, watch spring like scrolls with
6 to 9 identical, internal leaves. German scroll has been the standard
style of scroll decoration on Austrian and German arms for over 100
years. This style is similar to what British engravers call large
scroll. German speaking engravers refer to this style of ornamentation
as Neuenglische Arabesken.
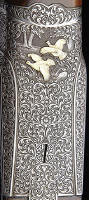
At left is pictured a close up of a typical, single "German" scroll
from an Austrian shotgun. At right is shown the floor plate of a highly
ornate German shotgun featuring profuse treatment with Neuenglische
Arabesken or "German" scroll.
|
GLENDO CORP./GRS – A manufacturer and distributor of tools and
accessories for hand engravers and jewelers. Located in Emporia,
Kansas, USA, GRS founder Don Glaser co-invented the Gravermeister™ and
was involved in the development of other air impact engraving tools
manufactured by GRS.
|
GLENSTEEL™ - A proprietary high speed steel alloy used in graver
blanks manufactured and sold by GRS Engraving Tools of Emporia, Kansas.
|
GLIDE-LOCK™ VISE – A highly sophisticated and finely machined
engraver’s block designed and manufactured by Steve Lindsay Tools and
Engraving in Kearney, Nebraska.
http://www.handengravetools.com/vises.htm
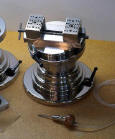
|
GOLIATH VISE - The Goliath 4140 Chrome-Moly Vise is a
precision-machined vise manufactured by Steve Lindsay Tools and
Engraving in Kearney, Nebraska.
http://www.handengravetools.com/vises.htm
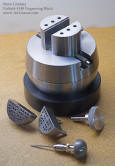
|
GOLDSMITH - An artisan who makes jewelry and other objects out
of gold or other precious metals. A master goldsmith must be proficient
at engraving as well as casting, designing, forming, piercing,
polishing, soldering, and stone setting among other things.
|
GOLDTAUSCHIERUNG – German speaking engraver’s term for the
inlaying of precious metal, particularly gold.
|
GOTHIC - Outside the USA Gothic script is also known as
Blackletter or Gothic minuscule, which was a script (or family of
scripts) of the Latin alphabet used throughout Western Europe from
approximately 1150 to 1500. It continued to be used for the German
language until the twentieth century. Blackletter is sometimes called
Old English, but it is not to be confused with the Old English
language.
Within the USA "Gothic" is another name for sans-serif typefaces which
do not have the small features called "serifs" at the end of strokes.
The term comes from the French word sans, meaning "without".
The gothic letter, sometimes-called block letters, are constructed of
strokes relatively even in weight. Slightly thinner strokes join main
stems and curves to avoid giving the letter a dense look.
Gothic, Blackletter, and Old English, along with Roman and script are
the most common styles of lettering cut by hand engravers worldwide.
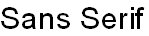
|
GRAPE LEAF – Ornamentation, which incorporates swirling vines,
grape leaves and grapes in a stylized pattern. Grape leaf is one of the
less frequently encountered styles of gun engraving that was more
popular in the 19th century.
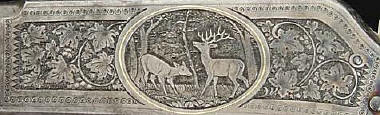
Pictured is an example of grape leaf scroll framing a game scene on an
antique Marlin lever action rifle.
|
GRAND MASTERS – An annual engraving workshop sponsored by the
GRS Corp. that features two internationally renowned "Grand Master"
engravers. Each master teaches a five day workshop to experienced
engravers who have been selected based upon their past work and
potential ability to absorb a high level of instruction.
|
GRAVER – A general term used for any tool made to engrave metal.
Traditional gravers have a blade type shape and are manufactured in a
variety of point types that include, bevel, flat, knife, lozenge,
onglette, oval, round, and square. Traditional gravers are available in
both tool steel and high-speed steel.
Today many engravers use 3/32” round or square gravers that they shape
to their needs using a sharpening fixture or sharpening template. This
type of graver is particularly popular with engravers using powered,
freehand engraving tools though such gravers are often used in burin
handles and chisel handles as well.
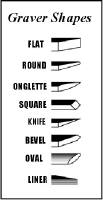
|
GRAVER BLANK – An un-ground, un-sharpened graver. A graver blank
may be either of the traditional blade style or 3/32” round or square
stock. Graver blanks are made of either carbide, C-Max™, Glensteel™,
tungsten carbide, tool steel, high speed steel, Lindsay Carbalt™,
Lindsay M42™, Mo-Max™ cobalt, or X7™. Trade names on graver blanks
include Gesswein, Grobet, GRS, Lindsay, Mo-Max, Muller, and Vallorbe.
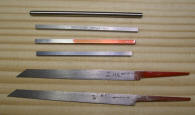
Pictured is an assortment of graver blanks. From top the blanks are
round, 3/32" square, and traditional.
|
GRAVERMACH™ – A freehand engraving system that is powered by
compressed air and contains a spring-loaded piston within a hand piece
of various size and shape, depending upon intended use. The Gravermach™
is capable of 400 to 8000 strokes per minute operating speed, however
the handpieces it operates are only capable of 4000 and uses a
dual-stage regulator. The impact power is regulated via a progressive
foot control. The Gravermach™ is generally, a more sophisticated and
costly version of the Gravermax™. There are five components to a
Gravermach™ system: control box, hand piece, a graver, foot control,
and air compressor.
The Gravermach™ is not an “engraving machine” in the sense that it is
completely controlled free hand by the engraver. Its main advantage
over hammer & chisel is that the piston within the hand piece takes the
place of a chasing hammer thus freeing one of the engraver’s hands to
turn the engraving block as well as greater control of the graver than
can be supplied by manual power alone.
Manufactured by the GRS Corp of Emporia, Kansas.
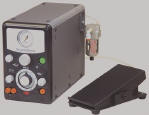
|
GRAVERMAX SC™– A freehand engraving system that is powered by
compressed air and contains a spring-loaded piston within a hand piece
of various size and shape, depending upon intended use. The Gravermax™
uses a single-stage air regulator. The impact power is regulated via a
progressive foot control. Generally, a simpler and less costly version
of the Gravermach™. There are five components to a Gravermax system:
control box, hand piece, a graver, foot control, and air compressor.
The Gravermax™ is not an “engraving machine” in the sense that it is
completely controlled free hand by the engraver. Its main advantage
over hammer & chisel is that the piston within the hand piece takes the
place of a chasing hammer thus freeing one of the engraver’s hands to
turn the engraving block as well as greater control of the graver than
can be supplied by manual power alone.
Manufactured by the GRS Corp of Emporia, Kansas.
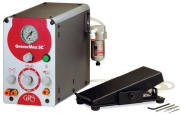
|
GRAVERMEISTER™ – The trade name for the first pneumatic-powered
freehand engraving tool. Engravers John Rohner and Don Glaser developed
the Gravermeister™. The device uses an ordinary graver set in a hand
piece that is connected to a length of pneumatic tubing. The tubing is
connected to a vacuum motor that provides an alternating pulse of
suction, which draws back a piston against a spring within the hand
piece then releases it. The Gravermeister™ differs from more modern and
advanced air powered hand engraving devices in that it does not require
a source of compressed air from an air compressor or pressurized tank.
Four components are required to engrave with a Gravermeister, the
vacuum pump unit, hand piece, a graver, and foot control.
The Gravermeister™ is not an “engraving machine” in the sense that it
is completely controlled free hand by the engraver. Its main advantage
over hammer & chisel is that the piston within the hand piece takes the
place of a chasing hammer thus freeing one of the engraver’s hands to
turn the engraving block as well as greater control of the graver than
can be supplied by manual power alone.
Manufactured by the GRS Corp of Emporia, Kansas.
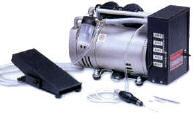
|
GRAVEURKUGEL – German: Literally, engraving ball. A “block” or
engraver’s block.
|
GRECIAN FRETS – See
FRETWORK.
|
GRIFFIN – A mythical creature, part eagle and part lion,
sometimes used as an engraved motif, especially pre-20th century.
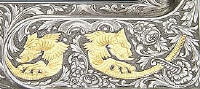
|
GRIP SHIELD – The portion of a single action revolver,
particularly a Colt Single Action Army or copies thereof, which is
connected to the top of the back strap and is in the shape of a shield.
The grip shield of a revolver is often the subject of engraved
ornamentation or a motif.
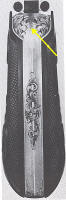
Pictured is the grip shield (arrow) and backstrap of a Colt SAA
engraved by Ken Hurst of North Carolina in the 1970's.
|
GROTESQUE – A decorative motif characterized by fanciful or
fantastic human and animal forms, often interwoven with foliage or
similar figures; the natural may be distorted into absurdity, ugliness
or caricature. Grotesques were especially popular with arms
embellishers from the 17th through the 19th centuries. At one time the
province of European engravers, grotesques are now occasionally found
engraved by Americans. Italian engravers use the term: Macherone.
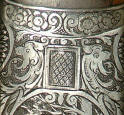
Pictured is a flush gold inlayed grotesque on a knife by Steve Lindsay
and a pair of line cut grotesques on the floor plate of a German
Gustloff shotgun.
|
GUILLOCHE – In ornamental art, any pattern made by interlacing
curved lines. Guilloché is an engraving technique in which a very
precise intricate repetitive pattern or design is mechanically etched
or cut into metal with very fine detail. Specifically, it involves a
technique of engine turning, called guilloché in French after the
French engineer “Guillot”, who invented a machine “that could scratch
fine patterns and designs on metallic surfaces.” The machine improved
upon the more time-consuming practice of making similar designs by
hand, allowing for greater delicacy, precision, and closeness of the
line, as well as greater speed. Guilloche patterns are often found
engraved into the cases of antique pocket watches and in the underlying
metal of objects covered with translucent vitrified enamel. Guilloche
patterns are frequently engraved into banknote printing plates by the
use of a cycloidal engine thereby making the printed notes difficult to
counterfeit.
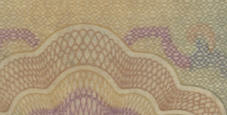
Pictured at left is an object engraved with a guillouche pattern and
overlaid with translucent blue vitreous enamel. Next are two discs
engraved with guilloche patterns and last a banknote printed from a
plate engraved with guilloche tracery.
|
GUN ENGRAVING – In the US, Great Britain, and Europe, gun
engravers make up the majority of master level hand engravers who are
skilled at all allied facets of the engraver’s art. To be considered a
master level gun engraver, one must be proficient in the design and
execution of: numerous varieties of traditional scroll and border work,
precious metal inlay and overlay, sculpted relief figures, scenes, and
scrollwork, banknote, line cut and bulino scenes and figures as well as
lettering.
The gun engraver must also have an understanding of the function of
different gun parts and be able to have good tool control on the
complex convex, concave, and flat surfaces of guns. In the US, most
freelance gun engravers work for an aftermarket where they are given
guns to engrave that are already hardened, finished, and assembled. As
a result they must have some gunsmithing skills to disassemble, strip
the finish, anneal the metal when necessary or be able to engrave in
the hardened state then refinish and reassemble the gun.
In Great Britain and Europe, gun engravers usually work for gun
factories or cottage industry gunmakers who provide the gun parts
pre-hardened and disassembled, as do American factory gun engravers.
Forty years ago the skills of the hand engraver were rapidly becoming a
dieing art. Hand engraving was being supplanted in die making by
progressively more sophisticated 3 dimensional milling pantographs,
which are today controlled by computers. In the jewelry, tableware, and
award businesses where most call for engraving was in the form of
lettering, inscriptions, and monograms, the relatively inexpensive
manual diamond drag pantograph displaced the hand engraver. And the
once fertile field of work for watch case engravers had long since died
as the mass-produced wristwatch replaced the pocket watch.
At that low point in the history of hand engraving it was only the gun
engravers who were keeping the art alive. There were two reasons for
this. First, the surfaces of a firearm were too complex in nature to
adapt machinery meant for work only on flat surfaces, which even if it
could be adapted, could not produce the kind of cuts available to the
hand engraver. Secondly, gun collectors and those who use expensive
engraved guns tend to be highly traditional in their view of things
connected with guns and therefore disdained mass-produced decoration.
Even then by the 1960’s there were only a small number of gun engravers
left in the United States.
A renaissance of hand engraving began in the late 1960’s to early
1980’s. This was the result of the convergence of three things. First
was the publication of important and motivating works on the subject of
gun engraving. In 1965, author and gun historian R. L. Wilson complied
the engraving record of 19th century gun engraver L. D. Nimschke into a
well-received book. Then well-known engraver Jack Prudhomme wrote a
book entitled “Gun Engraving Review” which coincided with an exhibition
of his work at the Norton Art Gallery. At the same time John Amber, the
editor of the “Gun Digest” featured engraving prominently in all his
publications. Then designer/engraver James B. Meek wrote a most
comprehensive how to book entitled “The Art of Engraving” (which is
still in print today).
The second thing of significance was the invention of the first
practical and successful power operated, freehand engraving tool known
as the Gravermeister which is pneumatic and works off of a vacuum pump.
The Gravermeister was followed into production by the NgraveR later
known as the Magnagraver that operates off of an electric motor
connected to a flex-shaft. These two engraving tools along with Meek’s
book opened the door to hand engraving to many in the US who had
struggled trying to learn hammer & chisel or burin engraving without
any means of personal instruction.
The third thing in this chain of events was the founding of the
Firearms Engravers Guild of America (FEGA) in 1980 that coincided with
the publication of “American Engravers” by a relatively new engraver
named Roger Bleile. From a formational meeting of 21 engravers, FEGA
has grown into an organization of over 600 engravers worldwide.
As a result of these three things more and varied books were published
on the subject of gun engraving in English, French, Italian, and
German. As engravers matured, training classes began to proliferate
around the US with the most prominent at GRS headquarters in Emporia
Kansas. These classes became a magnet for those who wished to revive
the engraving arts outside the field of guns thus hand engraved
jewelry, knives and even motorcycles and custom cars became part of the
engraving renaissance.
Today with Internet tools like this glossary and hand engraving forums
as well as highly sophisticated freehand engraving tools like the
Lindsay Palm Control and Gravermach, the art of hand engraving is not
only alive but thriving with engravers and patrons of the art.
|
|